Definition and characteristics
Concentrate is the final product obtained after ore is crushed, ground, sorted and other processes. In this process, the useful minerals in the ore are enriched, while the gangue and impurities are mostly removed. The characteristics of concentrate are its high grade and high value, which makes it more efficient and economical in the subsequent smelting and processing.
Middlings are intermediate products obtained in the sorting process. It usually consists of concentrates from scavenging operations and tailings from beneficiation operations. The grade of middlings is generally between the final concentrate and tailings grades, so it usually needs to be returned to an appropriate operation point for re-selection or separate treatment. The existence and treatment of middlings are of great significance to improving the overall beneficiation efficiency and recovery rate.
Tailings are the remaining part of the ore that is no longer recycled after the main useful components have been enriched in the concentrate after the sorting operation. Tailings usually still contain a certain amount of minerals with recycling value, but they are temporarily discarded due to the limitation of the technical level in a certain period of time or the high cost of continued recycling. However, with the advancement of technology and the improvement of environmental awareness, the reuse and recovery of tailings has become an important research direction.
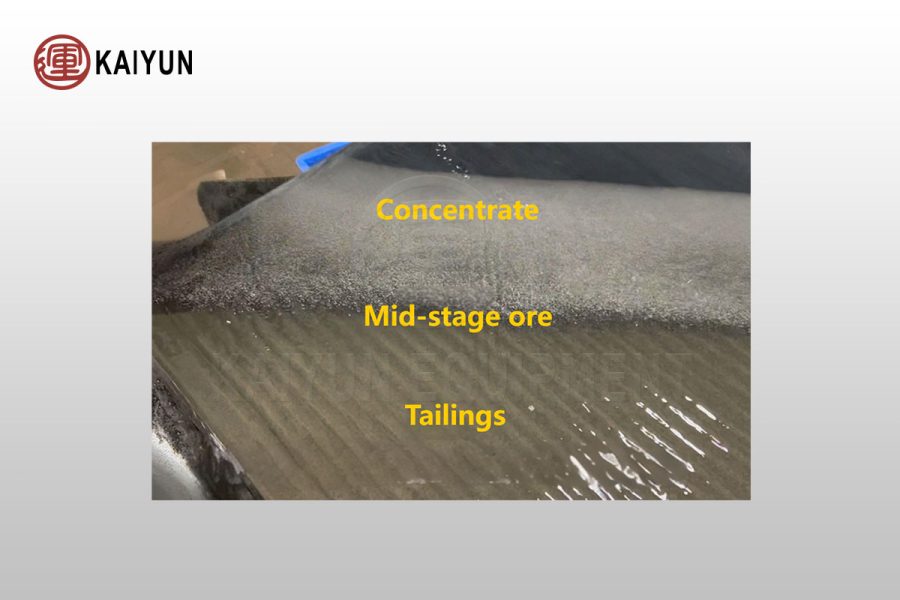
Relevant indicators of concentrate
In order to evaluate the quality of concentrate and the efficiency of the mineral processing process, we need to use a series of relevant indicators. These indicators include yield, recovery rate, mineral processing ratio, rich ore ratio, particle size recovery rate, metal distribution rate and mineral processing efficiency.
Yield
Yield refers to the percentage of the weight of a certain product to the weight of the original ore in the mineral processing process. It is an important indicator to measure the output of the product in the mineral processing process. The calculation formula of yield is: yield = weight of a certain product/weight of the original ore × 100%.
Recovery rate
The recovery rate refers to the percentage of the weight of the metal or other useful components in the concentrate product to the weight of this substance in the original ore. It is an important indicator reflecting the degree of recovery of metals (or other useful components of recovery rate) in the mineral processing process, the level of mineral processing technology, and the quality of management work. The calculation formula of recovery rate is: recovery rate = weight of a metal in concentrate / weight of the metal in the original ore × 100%.
Recovery rate can also be divided into actual recovery rate and theoretical recovery rate. The actual recovery rate is calculated based on actual production data, while the theoretical recovery rate is calculated based on theoretical optimal conditions. By comparing the actual recovery rate and the theoretical recovery rate, we can evaluate the efficiency and potential of the mineral processing process.
Mineral processing ratio
The mineral processing ratio refers to the ratio of the amount of original ore to the amount of concentrate, or the number of tons of original ore required to select one ton of concentrate. It is an important indicator for measuring the consumption of original ore in the mineral processing process. The calculation formula of mineral processing ratio is: mineral processing ratio = amount of original ore / amount of concentrate.
Rich ore ratio
The rich ore ratio refers to the ratio of the grade of a useful mineral in the concentrate to the grade of the original ore, that is, the grade of the concentrate is several times the grade of the original ore. It is an important indicator for measuring the enrichment of the concentrate. The calculation formula of the rich ore ratio is: rich ore ratio = concentrate grade / original ore grade.
Particle size recovery rate
Particle size recovery rate refers to the recovery rate of metal (or other useful components) of a certain particle size in the concentrate. It is used to analyze the reasons for the high and low recovery rates in order to better optimize the mineral processing process. The calculation formula of particle size recovery rate is the same as the above recovery rate calculation formula, except that the calculation range needs to be limited to a certain particle size.
Metal distribution rate
Metal distribution rate refers to the percentage of the amount of metal in each product to the amount of metal in the original ore during the mineral processing process. It is used to indicate the distribution of metals in each product. The operating metal distribution rate refers to the ratio of the amount of metal in a certain operating product to the amount of metal in the operating feed ore. The metal distribution rate has the same meaning as the recovery rate, but the difference is that it focuses more on describing the distribution of metals in each product.
Mineral processing efficiency
Mineral processing efficiency is also called sorting efficiency. It indicates the ratio of the increase in the amount of useful minerals or metals in the concentrate during the mineral processing process to the increase under the assumed optimal conditions. It is a comprehensive indicator for evaluating the quality of the mineral processing process. The calculation formula for mineral processing efficiency is relatively complex and involves multiple parameters and variables. But in general, it reflects the growth of useful minerals or metals in the mineral processing process and the level of mineral processing technology.
Optimization and improvement in the mineral processing process
In order to improve the quality of concentrate and the efficiency of the mineral processing process, we need to optimize and improve the mineral processing process. This includes the following measures:
Improve the level of mineral processing technology
By introducing advanced mineral processing technology and equipment, and improving the automation and intelligence level of the mineral processing process, the quality and recovery rate of the concentrate can be significantly improved. At the same time, it can also reduce energy consumption and costs and improve economic benefits.
Strengthen ore pretreatment
Ore pretreatment is of great significance to improving mineral processing efficiency and quality. Through reasonable crushing, grinding and grading processes, the useful minerals in the ore can be more fully exposed, thereby improving the mineral processing effect.
Optimize the mineral processing process
By optimizing the mineral processing process, the amount of middlings and tailings can be reduced, and the output rate and recovery rate of the concentrate can be increased. At the same time, it can also reduce energy consumption and costs and improve overall economic benefits.
Strengthen the comprehensive utilization of tailings
With the advancement of technology and the improvement of environmental awareness, the comprehensive utilization of tailings has become an important research direction. By adopting advanced processes and technical means, useful minerals in tailings can be recovered and utilized, thereby maximizing the utilization of resources and protecting the environment.
Strengthen the management and monitoring of the mineral processing process
Strengthening the management and monitoring of the mineral processing process is an important means to improve the efficiency and quality of mineral processing. By establishing a sound management system and technical standard system, strengthening the monitoring and control of the mineral processing process, problems can be discovered and solved in a timely manner to ensure the stability and reliability of the mineral processing process.